1. Requirements for gate location
1. Appearance requirements (gate marks, weld lines)
2. Product functional requirements
3. Mold processing requirements
4. Warpage of the product
5. The gate volume is not easy to remove
2. Impact on production and function
1. Flow Length (FlowLength) determines the injection pressure, clamping force, and the shortening of the full flow length when the product is not filled can reduce the injection pressure and clamping force.
2. The position of the gate will affect the holding pressure, the size of the holding pressure, and whether the holding pressure is balanced. Keep the gate away from the future force position of the product (such as the bearing) to avoid residual stress. The gate position must be considered for exhaust. To avoid wind accumulation, do not place the gate at the weak or embedded part of the product to avoid deviation (CoreShaft).
Three, the skill of choosing the gate location
1. Place the gate at the thickest part of the product, and pouring from the thickest part can provide better filling and pressure holding effects. If the holding pressure is insufficient, the thinner area will solidify faster than the thicker area. Avoid placing the gate at a sudden change in thickness to avoid hysteresis or short shots.
2. If possible, pouring from the center of the product. Placing the gate in the center of the product can provide equal length flow. The size of the flow length will affect the required injection pressure. The central pouring makes the packing pressure uniform in all directions. Can avoid uneven volume shrinkage.
3. Gate: The gate is a short groove with a small cross-sectional area to connect the runner and the mold cavity. The cross-sectional area is therefore small in order to obtain the following effects:
1) Soon after the cavity is injected, the gate will be cold
2) Easy to remove water
3) The dewatering port is completed, leaving only a few trace
4) Make the filling of multiple mold cavities easier to control
5) Reduce the phenomenon of excessive filler
There are no hard and fast rules for the method of designing gates. Most of them are based on experience, but there are two basic elements that must be compromised:
1. The larger the cross-sectional area of the gate, the better, and the shorter the length of the channel, the better, in order to reduce the pressure loss when the plastic passes. WeChat of the mold master: mujudaren
2. The gate must be narrow to facilitate cold formation and prevent excessive plastic from flowing back. Therefore, the gate is in the center of the runner, and its cross-section should be as circular as possible. However, the gate switch is usually made of a module Switch to decide.
3. Gate size:
The size of the gate can be determined by the cross-sectional area and the length of the gate. The following factors can determine the best size of the gate:
1) Rubber flow characteristics
2) The thickness of the module
3) The amount of rubber injected into the cavity
4) Melting temperature
5) Mold temperature
When deciding the location of the gate, the following principles should be adhered to:
1. The rubber injected into each part of the cavity should be as even as possible.
2.The rubber material injected into the mold should maintain a uniform and stable flow frontline at all stages of the injection process.
3. The possible occurrence of weld marks, bubbles, cavities, vacant positions, insufficient glue and glue spray should be considered.
4. The operation of the dewatering port should be made as easy as possible, preferably automatic operation.
5. The position of the gate should be matched with all aspects.
Fourth, the balance of the gate
If a balanced runner system cannot be obtained, the following gate balance method can be used to achieve the goal of uniform injection molding. This method is suitable for molds with a large number of cavities. There are two ways to balance the gate: changing the length of the gate channel and changing the cross-sectional area of the gate. In another case, that is, when the mold cavity has a different projected area, the gate also needs to be balanced. At this time, to determine the size of the gate, you must first determine the size of one of the gates and find its corresponding The ratio of the cavity volume comparison, and applying this ratio to the comparison between its gate and each corresponding cavity, the size of each gate can be obtained one after another. After actual trial injection, the balance of the gate can be completed operating.
Five, the position of the gate in the runner
When the plastic flows into the runner, the plastic is the first to reduce heat (cooling) and solidify when it approaches the mold surface. When the plastic flows forward, only the solidified plastic layer flows through. Also because the plastic is a low heat transfer substance. Solid plastic is formed. The insulating layer and the retaining layer can still flow. Therefore, under ideal circumstances, the gate should be set at the position of the cross runner layer to achieve the best plastic flow effect. This situation is most common in circular and hexagonal cross runners. However, the trapezoidal cross runner cannot achieve this effect, because the gate cannot be set in the middle of the runner.
Six, direct gate (DirectGate) or sprue gate (SprueGate)
The sprue directly supplies the plastic to the finished product. The sprue adheres to the finished product. In the two-plate mold. The large nozzle is usually one out, but in the design of the three-plate mold or hot runner mold, one can be used. A lot of beer.
Disadvantages: the formation of nozzle marks on the surface of the finished product will affect the appearance of the finished product. The size of the nozzle mark lies in the small diameter hole of the nozzle.
7. The ejection angle of the nozzle and the length of the nozzle
Therefore, the large nozzle mark can be reduced, as long as the delay of the above-mentioned nozzle is reduced. However, the diameter of the nozzle is affected by the diameter of the furnace nozzle, and the nozzle must be easy to be ejected from the mold, and the ejection angle cannot be less than 3 degrees. Only the length of the nozzle can be shortened, just use a longer nozzle.
Gate selection: The gate is the connecting part of the runner and the cavity, and also the last part of the injection mold feeding system. Its basic functions are:
1) Make the molten plastic from the runner enter the filling cavity at the fastest speed.
2) After the cavity is full, the gate can be quickly cooled and sealed to prevent the cavity from returning to the uncooled plastic.
8. Summary
The design of the gate is related to the size of the plastic part, the shape of the mold structure, the injection process conditions and the performance of the plastic part. However, according to the basic functions of the above two sentences, the gate section is small and the length is short, because only in this way can the increase be satisfied. Large flow rate, fast cooling and sealing, easy to separate plastic parts and minimum gate residues.
The main points of gate design can be summarized as follows:
1. The gate is opened in the thicker section of the plastic part, so that the melt flows from the thick section to the thin section to ensure complete mold filling;
2. The choice of gate position should make the plastic filling process the shortest to reduce pressure loss;
3. The selection of the gate position should help to eliminate the air in the cavity;
4. It is not advisable for the gate to rush the melt directly into the cavity, otherwise it will produce a swirling flow, leaving swirling marks on the plastic part, especially the narrow gate is more prone to such defects;
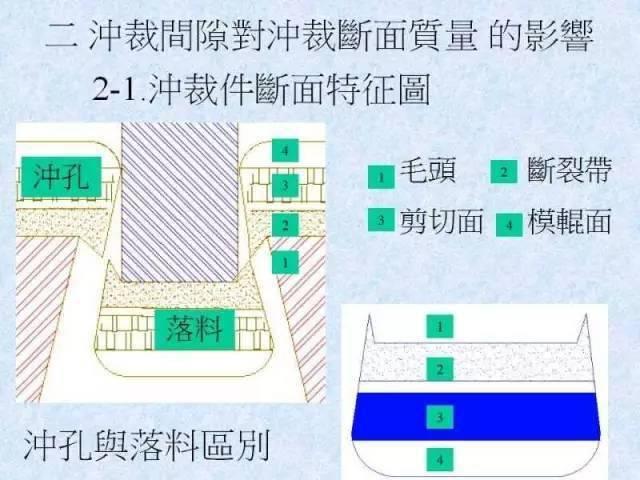