The core structure of in-mold tapping technology revealed!
Many years ago, in-mold tapping was still in the confidential stage, which is really the
core of foreign technology. Today, I will announce a detailed in-mold tapping structure
and installation process for everyone to learn and refer to.
Common mold design methods for in-mold tapping machines, and the installation method of
in-mold tapping machines are as follows:
1. Installation method of floating plate
For tapping on flat products, the structure used for screws above M1.5 can choose top-down
tapping or bottom-up tapping.
2. Installation method of stripping board
Tapping in the product pit, or the feeding direction has screw holes on the level or
difference surface, and screw holes of small size screws below M1.5.
Choose the floating board installation method. The product is characterized by flat
tapping, and the tapping part in the conveying direction of the material belt has no
protrusions.
Three, the main points of attention in the mold design of the floating plate installation
method
It is mainly the design of the mould lifting plate, which should be synchronized with the
movement of the lifting pin. The main body of the in-mold tapping machine is installed on
the floating plate, and the main body of the in-mold tapping machine is supported by the
floating plate.
The lifter pin is pressed down by the stripper plate, and the lifter plate is pressed down
by the stripper plate or by adding a nitrogen spring. The lifting plate is required to be
synchronized with the movement of the lifting pin.
With bottom-up tapping, the position where the mold needs to be avoided is as follows:
The specific structure of the upper mold base installation mold tapping machine screw
position, connection screw hole and pin hole position is as follows:
The specific structure of the tapping machine screw position, connecting screw hole and
pin hole position of the lower mold base is as shown in the figure below:
The specific structure of the screw position of the tapping machine in the mounting mold
of the floating plate, the connection screw hole and the pin hole position are as follows:
After summarizing, the installation sequence of the floating plate and the movement
process of the mold. The details are as follows:
While tapping the mold from the bottom up to avoid the position. The details are as
follows:
4. Bottom-up tapping stripping board installation method
1. Choose the installation method of the stripping board:
Product features: The tapping part of the belt conveying direction is convex or concave.
Screw specifications below M1.5
2. Main points of attention in mold design:
Mainly the design of mold mounting plate and floating plate: the floating plate should be
synchronized with the movement of the floating pin. The main body of the in-mold tapping
machine is installed on the mounting plate, and the mounting plate and the main body of
the in-mold tapping machine are supported by the floating plate.
The stripper plate presses down the floating pin, and simultaneously presses down the
floating plate or increases the nitrogen gas spring to press down at the same time. It is
required that the lifting plate should be synchronized with the movement of the lifting
pin.
The floating plate should be synchronized with the movement of the floating pin. The body
of the in-mold tapping machine is installed on the mounting plate, and the mounting plate
and the body of the in-mold tapping machine are supported by the floating plate.
The stripper plate presses down the floating pin, and simultaneously presses down the
floating plate or increases the nitrogen gas spring to press down at the same time. It is
required that the lifting plate should be synchronized with the movement of the lifting
pin.
After summarizing, the installation sequence of the floating plate and the movement
process of the mold. The details are as follows:
For in-mold tapping, it is now very popular. The designer mainly reserves space for the
tapping machine, and then installs a special tapping machine staff to cooperate and
complete it.
Today's in-mold tapping is a very common application technology, and it has also been
widely used in all walks of life.
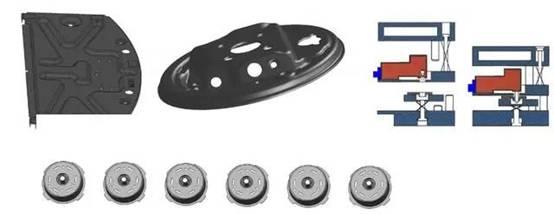